板金絞り加工とは?種類や工程、ヘラ絞り加工との違いについて解説!
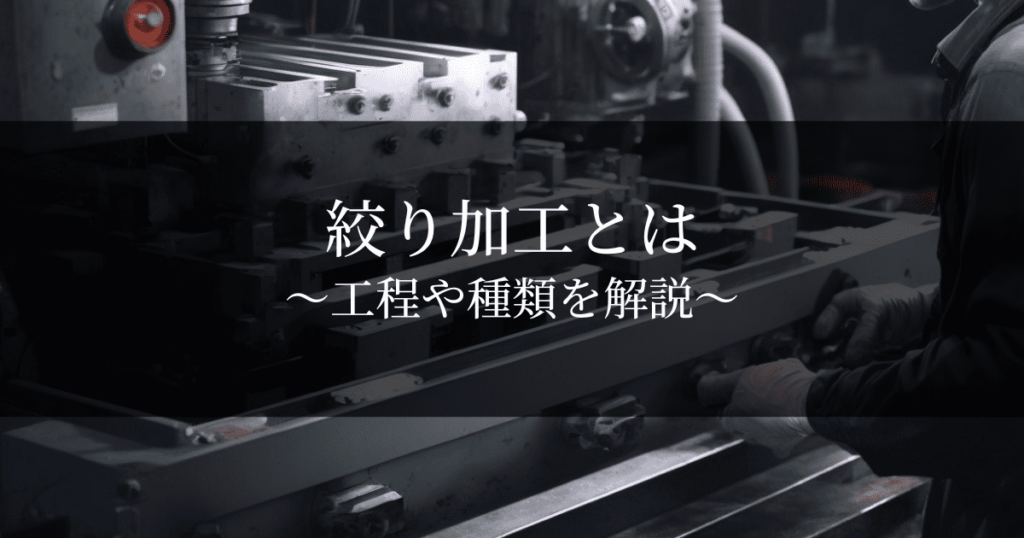
板金・プレス加工には「せん断加工」「曲げ加工」「絞り加工」「成形加工」「圧縮加工」の5種類があります。
この記事ではその中の絞り加工について解説しています。
絞り加工の種類や工程、ヘラ絞り加工との違いなどについてまとめました。
なお、板金加工またプレス加工については以下の記事で全般的に解説しています。
▼板金加工について解説している記事
板金加工とは?特徴や種類・加工工程やプレス加工との違いなどを解説
▼プレス加工について解説している記事
プレス加工とは?メリットやデメリット・加工方法・板金などとの違いを紹介!
目次
絞り加工とは
絞り加工とは、金属製品を製作するためのひとつの方法です。
プレス機で、金属板をパンチでダイに押し込み、底があって継ぎ目がない、カップ状や箱状に成形する加工方法のことを指します。
絞り加工は、板材の形状を自由に変えることができるため、多種多様な製品や部品を製作する際に利用されています。
具体的には、鍋やシンク、自動車のボディなどです。
このように絞り加工は、私たちが日々の生活の中でよく目にする多くの製品や部品に利用されています。
絞り加工の工程
絞り加工の工程は、基本的には以下の4つのステップからなります。
①板材をセットする
最初のステップは、まずダイに板材をセットします。
製作する製品や部品の形状、また強度などに応じて選択した板材を、適切な位置にセットします。
このとき、シワ押さえ板で板材を固定します。
②板材をパンチでダイに押し込む
次のステップは、パンチで板材を押し込みます。
板材をシワ押さえ板で制御しながら、外周部を中心に引き込むようにして、ダイに押し込みます。
なお、シワ押さえ板で固定した部分も引き込むため、板材の厚みは変わりません。
③絞り加工を繰り返す
製作する製品や部品の深さが長い場合は、絞り加工を複数繰り返す必要があります。
これは、一度の絞り加工で絞れる径や深さには限界があるためです。
ちなみに一回目の絞り加工を初絞り、二回目以降の絞り加工を再絞りと言います。
④トリミング加工
最後のステップは、絞り加工を行った製品や部品の余分な部分、つまりフランジを取り除きます。
これはトリミング加工と言います。
以上が絞り加工の基本的な工程です。
絞り加工の種類
絞り加工の種類は、製品や部品の完成品の形状と深さ、また方法によっていくつかに分けられます。
形状の種類
まずは形状によって分けられる種類について解説します。
- 円筒絞り
- 角筒絞り
- 異形絞り
- 円錐絞り
- 角錐絞り
- 球頭絞り
円筒絞り
円筒形状の製品や部品を製作するための絞り加工です。
基本的な種類で、板材に対して均等に力が加えられるため、成形が安定します。
飲み物の缶や一部の自動車部品などで用いられています。
角筒絞り
角筒形状の製品や部品を製作するための絞り加工です。
円筒絞りと比較すると、板材をパンチでダイに押し込むとき、角部分と辺部分で異なる動きをするため、難易度が高い種類となります。
形状は箱状となるため、ケースなどを製作する際に用いられます。
異形絞り
一般的な円筒や角筒のような形状に当てはまらない、特殊な形状の製品や部品を製作するための絞り加工です。
なお、金型のイニシャルコストがかかるうえ、さまざまな方向に力がかかるため難易度も高くなります。
特殊な形状のハウジングを製作する際などに用いられます。
円錐絞り
円錐形状の製品や部品を製作するための絞り加工です。
側面にテーパーをつける種類となっています。
円筒絞りの変化形で、難易度は高いです。
角錐絞り
角錐形状の製品や部品を製作するための絞り加工です。
円錐絞り同様、側面にテーパーをつける種類となっています。
加えて、角錐絞りは側面が平面な形状になることが特徴です。
球頭絞り
球頭形状の製品や部品を製作するための絞り加工です。
簡単に言うと、底面が半球の形状となる種類です。
パンチは使いますが、ダイを使わず液圧を利用するため、張り出し加工とも言います。
深さ別の種類
次に深さによって分けられる種類について解説します。
- 浅絞り
- 深絞り
浅絞り
製品や部品の深さが浅いものは、浅絞り加工と言います。
具体的には、完成品の直径よりも深さが長くないものが該当します。
深絞り加工と比較すると、工程が少ない点が特徴です。
身近なものでは、灰皿やフライパンなどが例としてあげられます。
深絞り
製品や部品の深さが深いものは、深絞り加工と言います。
具体的には、完成品の直径よりも深さが長いものが該当します。
絞り加工を複数繰り返す必要があり、浅絞り加工と比較すると工程が多くなるうえ、難易度も高い点が特徴です。
方法の種類
最後に方法によって分けられる種類について解説します。
- 温間成形法
- 対向液圧成形法
一般的には板材をパンチでダイに押し込み形状を成形するという方法ですが、これらは少々特殊な方法となっています。
温間成形法
温間成形法とは、板材を加熱しながら絞り加工を行う方法です。
金属は加熱させることで加工性が向上しますが、これを利用した方法が温間成形法となります。
加工性の低い、アルミやステンレスなどの合金を絞り加工する際に向いています。
これにより、冷間では限界だった深さの深絞り加工を行うことが可能となります。
また、工程を少なく済ませられるようになることもメリットのひとつです。
しかし、金型や設備といった初期費用は高くなります。
対向液圧成形法
対向液圧成形法とは、仕組みとしては一般的な絞り加工と同じです。
しかし、パンチは使うものの、ダイは使わず液圧を利用する点で異なります。
対向液圧成形法では、パンチを押し込むと同時に下からの液圧が発生して、これにより板材がパンチに押し込まれて成形されます。
この方法では、板材に対して均等に力を加えられるため安定した成形を行うことが可能なうえ、これによりより深く深絞り加工を行うことも可能です。
また、複雑な形状にも対応でき、ワレやシワ、キズといったトラブルの発生を防ぐこともできます。
さらに、ダイを不要とするため金型の初期費用を安く済ませられるメリットもあります。
しかし、液の注入や排出が必要となるため、生産効率の面ではデメリットがあると言えます。
ヘラ絞り(スピニング)加工との違い
この記事では、プレス加工における絞り加工について解説してきました。
しかし、絞り加工にはヘラ絞り加工という方法もあります。
これは、回転する板材に工具を押し当てながら成形する加工方法です。
押し当てる工具はヘラと呼ばれ、人の手で塑性変形を局所的に繰り返す仕組みとなります。
そんなヘラ絞り加工は、プレス加工における絞り加工と比較すると、小さな力を何度も加えることになるため、精密かつ複雑な形状の製品や部品を製作することが可能です。
例をあげると、ロケットや新幹線の先端といったものの製作に利用されています。
このように、大型のものの製作に向いていることも特徴のひとつです。
ちなみに、NC制御されたスピニングマシンで行われる場合は、スピニング加工と呼ばれます。
そんなヘラ絞り加工、スピニング加工と、この記事で解説してきました板金・プレス加工における絞り加工の違いを以下にまとめました。
板金・プレス加工における絞り加工 | ヘラ絞り(スピニング)加工 | |
定義 | 板材に一定の力を加えて成形する | 板材に小さな力を何度も加えて成形する |
メリット | 大量生産に向いている 加工速度が速い |
精密かつ複雑な形状に成形できる 対応できるサイズの範囲が広い |
デメリット | 金型や設備が必要でコストと時間がかかる 難易度が高い |
大量生産に向いていない 作業者の技術に依存する |
適用される製品・部品 | 比較的シンプルな形状の製品や部品 | 精密かつ複雑な形状の製品や部品 また大型のもの |