【円筒研磨とは?】特徴と加工方法/仕組みを紹介
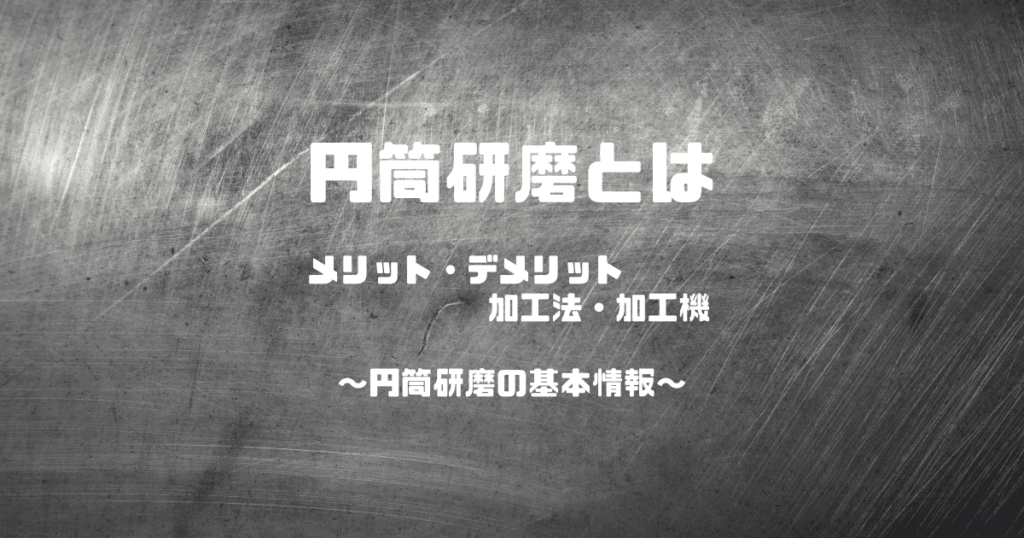
円筒研磨/研削とは、砥石を加工物に押し当て研磨/研削する方法で、筒状の外周を高精度に加工することができます。
加工物と砥石の両方を反対方向に回しながら擦り合わせます。
磨くような加工方法のため、切削取り代は少なく、取り代が少ない設定で威力を発揮します。
そのため、円筒研磨/研削は要求される加工精度が高い場合に使用します。
円筒研磨/研削を必要とする製品は通常、前工程に旋盤加工があります。
その場合は、旋盤加工だけで商品の要求精度(公差)を達成できるとコストダウンにつながります。
その意味で、「円筒研磨/研削は出来るだけ避けられる」ように旋盤工程での工夫が必要です。
機械加工の常識として、「旋盤・焼き入れ・研磨/研削」は、よくセットになる加工工程です。
大まかな加工を施し、研磨/研削で仕上げ加工をする感覚です。
「磨き上げる」と表現すればよいでしょうか。
ミクロン(μ:1/1,000mm)台の公差を実現するのに良い加工方法です。
目次
円筒研磨/研削のメリット「精度が命」
円筒研磨/研削工程の前には、旋盤工程がよくあります。
それは、円筒研磨/研削では多くの「取り代」が取れないため、おおむね旋盤で加工しておき、高精度に仕上げるのに円筒研磨/研削を使うことが多いからです。
そのため円筒研磨/研削の最大のメリットは、「高精度に仕上げる」ことです。
旋盤加工において、公差1μ(1/1,000mm)の精度はベテラン職人でなければ出せない精度です。
NC旋盤でも難しい精度です。
しかし、円筒研磨/研削ではかなり当然の精度です。
0.5μ程度まで自動機でも出すことが出来ます。
円筒研磨/研削のデメリット・注意点
円筒研磨/研削のデメリットと注意点をご案内します。
円筒研磨/研削のデメリットはコストが高いこと
円筒研磨/研削では取り代を大きくすることが出来ないため、前工程であらかじめある程度仕上げておくことが必要となり、二重工程でコストがかかることになります。
そこで、円筒研磨/研削は「高精度だからコストがかかる」、となるのです。
つまり、円筒研磨/研削のデメリットはコスト高であることです。
結果として、円筒研磨/研削が高精度仕上げ工程になり、部品製作工程では最終工程であることが多くあります。
円筒研磨/研削の注意点は過剰品質になりかねないこと
注意点の例を挙げると、「ブレーキディスクに鏡面加工の過剰品質」要求があった事例がありました。
自動車でも、陸上を走る他の乗物でも、ディスクブレーキが使われていることがあります。
完成して製品として使われればブレーキパッドで擦る部品であっても、設計では「▽▽▽(サンパツ仕上げ)以上の鏡面仕上げ」を、図面・SOP「標準作業手順書(Standard Operating Procedures)」で要求してしまっていたのです。
これは旋盤加工では実現できず、研磨/研削が必要となってしまいます。
よって、製品としては実現しておきたいのですが、「過剰品質」でありコスト高となってしまうのです。
とはいえ、コストを削減できれば円筒研磨/研削で鏡面仕上げとしたい部品であるのもまた事実なのですね。
円筒研磨/研削の狙い3つの高精度と注意点
円筒研磨/研削を行うのは、もちろん加工精度要求が高い場合ですが、どの様な場面で必要となるのでしょうか?
加工精度の高さが、円筒研磨/研削の必要性でもありメリットでもあります。
それは以下の3つの高精度を狙って加工されます。
高面粗度(鏡面加工)
面粗度とは加工面の粗さです。
機械加工では1ミクロンの加工精度を出すことは難しく、要求される加工精度次第で、研磨/研削工程を追加することがあります。
旋盤加工では、刃先の加減で平面に加工するのが難しい場合もあります。
通常、仕上げバイトの刃先のRを大きくして、送りを小さく下げて、刃物の切削跡を残さないようにすると、面粗度は上がります。
「▽▽▽(サンパツ仕上げ)」でも可能です。
注意点:工程が増え仕掛在庫が増える
しかし、送りを小さくすると時間がかかります。
刃先のRを多くするにも、やり過ぎると材質によっては「刃先のビビり」がでて、かえって面粗度が落ちてしまいます。
そこで円筒研磨/研削で砥石を押し付け、旋盤切削で出来た山を削って仕上げる方がコストダウンになる場合がでてきます。
この最大のデメリットは、切削時間が増えることよりも、工程が1段階以上増えるので、仕掛在庫が増えてしまうことです。
これが、円筒研磨/研削の工程カイゼンの方向性を示しています。
高精度寸法
円筒製品の外形寸法に+0.01以下の公差が指定されている高精度寸法の場合などは、円筒研磨/研削工程を経た方が品質が安定する可能性が高くなります。
砥石による円筒研磨/研削の取り代がμであるので、公差0.5μまで対応できる機械が多くあるからです。
注意点:前工程の加工精度
高精度を出すために円筒研磨/研削を使う場合、前工程で取り代をどの程度残すのかに注意が必要です。
取り代は少ない方が円筒研磨/研削では有利ですが、前工程に熱処理が入ることが多く、その歪に注目して旋盤工程で取り代を決める必要があります。
あまり旋盤工程で精度を高くしておくと、歪で製品にならなくなることが起きます。
高硬度材料研磨/研削
円筒研磨/研削と旋盤・焼き入れ工程が必要になる部品製作が多くあります。
それは高強度(高硬度・高靭性)を必要として、焼き入れを行う部品があるからです。
すると、旋盤工程で高精度を実現しても、高周波、浸炭焼き入れなどを行うと、熱による歪で寸法が狂ってしまうのです。
そこで、後工程の円筒研磨/研削で歪を修正するように仕上げることになります。
注意点:前工程との連携が重要
その時の前工程旋盤加工で、どれほどの取り代をどの程度残したらよいのかは、ノウハウとなります。
円筒研磨/研削により、時間がかからずコストがかさむことを抑えるのです。
そのとき重要なのは、旋盤、焼き入れ工程のような前工程との連携です。
歪を抑える焼き入れ作業となれば、旋盤で円筒研磨/研削での取り代を抑えても、不良品を出さずに完成品精度を保てます。
工程間の切削時間の平準化が出来ると、工程間在庫を抑えるのは楽になります。
センタレス研削のメリット
センタレス研削では「芯出し」が不要
円筒研磨/研削では、円筒研削盤が多く使われます。
この場合は製品の芯を抑えて、真円を出すのですが、取り付けで「芯出し」が必要になってきます。
焼き入れで歪が出た加工品、材料そのまま使用する直径の小さな丸棒などでは、「芯出し」が難しくなっており時間がかかってしまいます。
しかし、センタレス研削では「芯出し」が不要になり、大量生産方式に向いたメリットがあります。
「職人芸」と「量産品QCD」
製造業の加工には、目指すべき2つの方向性があります。
・1つは、「職人芸」と言われる、見事な作品です。
・もう一つは、「高精度・高品質」と「安く量産」です。商品価値の見方では、これに納期が加わります。
「ジャスト・イン・タイム」といわれてきましが、最近ではQCD「Quality(品質)、Cost(コスト)、Delivery(納期)」の3要素として取り上げているようです。
・この両方向があり、「量産品と手作り品」ともいえます。これら両方向で技術が違ってきますが、商品としては価格に現れてきます。「コストを下げて高品質」が目標なのですが、これにDelivery(納期)が加わってインダストリー4.0の動きになってきます。
・円筒研磨/研削では加工方法が2つありますが、芯出しの必要な円筒研削盤と必要のないセンタレス研削両方向の努力が続けられています。しかし、コストダウン、高資金効率を目指す方向性から見ると、「仕掛在庫削減」がカギとなります。量産企業では「資金効率」が絶対の条件で、その場合「仕掛在庫削減」は絶対の努力方向です。すると、「芯だし」のないセンタレス研削は加工時間の削減となり、加工品によっては大変有効な量産加工手段となります。
円筒研削盤の研削方法/注意点
円筒研削盤を使用して、よく行われる円筒研削の方法のそれぞれの特徴を見ておきましょう。
トラバース研削
製品(材料)をセンターで抑え、加工範囲の幅が砥石より広い時、当然、砥石を左右に振って円筒研磨/研削するしかありません。
それをトラバース研削と言います。
その研削方法の注意点、砥石の「突っ込み量」を全て取って、往復させるのか?砥石の「突っ込み量」を往復で分けて加工するのか?は、精度を出しやすくコストが削減できる方法をとるしかありません。
一般的には「粗びき・仕上げ」と往復で取り代に差を設けて、「突っ込み量」を変化させる方法でしょう。
また、横長加工物の研削注意点として、加工物の逃げを抑えることや、逃げを計算して砥石の「突っ込み量」を加減する必要が生じます。
つまり、左右の端よりも中央部分で加工物の逃げが大きくなるので、サポートが必要となります。
一般的には、両端と比べて中央部分で突っ込み量を多くして、研削結果として均一の外形を狙うことです。
「どのくらい?」となると、その作業のノウハウとなります。
プランジ研削
プランジ研削とトラバース研削の違うところは、砥石を左右に動かさずに真っすぐ突っ込ませることです。
そこで加工時には、第一に加工幅と砥石の幅とに注意して段取りします。
また、当然にトラバース研削以上に、加工物の逃げの量、横長や円筒直径との関係にも注意します。
アンギュラ研削
アンギュラ研削は、砥石を傾けて配置し、加工物を両方向に研削できることから、NC制御機械などによる段差や斜め研削、端面研削などに有効です。
しかし、砥石の角を使うことが多く、アンギュラ研削の注意点は、砥石管理が必要であることです。
円筒研磨/研削では加工精度が高いので、砥石の管理にノウハウが必要です。
円筒研磨/研削の目指す生産方式の方向
円筒研磨/研削のコストダウン、高資金効率には「工程結合」がよい
生産工程でのコストダウン、高資金効率を狙うときは、「工程結合」して「工程間在庫」を無くすことが、大幅な資金効率向上をもたらすことになります。
この最先端生産方式が「多種少量生産」「混流生産」で、基本は日本のトヨタ自動車が半世紀以上前から開発してきた「トヨタかんばん方式」です。
「リーン生産方式」としてアメリカに紹介されたものです。
この工程結合が円筒研磨/研削の場合でも採用される方向性です。
▼「行程結合」の方向性で造られた円筒研削盤の実例
“従来は研削全工程に円筒研削盤を3台要しますが、C6040Eは全工程を一挙に同時研削でき、設備台数1台で完結します。”
※引用PRTIMES(https://prtimes.jp/main/html/rd/p/000000287.000028729.html)
日本が開発した生産方式が、現在では自動車産業ばかりではなく、世界の量産工場では採用しなければ生き残れない方式となりました。
さらに、ネットの普及と共に「ネットショッピング」と結びつき、世界の製造業の存亡をかけた競争が続いています。
これは、インダストリー4.0(第四次産業革命)と言われています。
インダストリー4.0(第四次産業革命)
ドイツが国家を挙げて取り組んでおり、自動車メーカーのBMWは100を超えるオプションを自由に組み合わせてネットで発注すると、世界のどこでも2週間以内に納品できるシステムを実験してきました。
AIを使った生産管理システムで、世界の生産拠点を統合して、サプライヤーを含めて「混流生産」「順序生産」を実現していく方向性です。
この基本の製造技術、生産技術が、円筒研磨/研削においても目指すべき「工程結合」の方向性です。
それにはまず、「中間在庫を削減する」工夫を進めることです。
単に「専用機」にすればよいのではなく、トヨタ自動車の進めてきた「カイゼン」のノウハウを調べてみてください。
絶えず続いていく「カイゼン活動」の妨げにならない工程を考える必要があります。
まとめ
・円筒研磨/研削は「精度」が命で、メリット、デメリットは表裏一体です。
→メリットは高精度であり、デメリットは高コストです。しかしそれは表裏一体であり、生産方式のカイゼンを進める方向性が求められます。
・円筒研磨/研削はできるだけ行わない方が良い。
→コスト高となるので、仕上げ工程で必要になる円筒研磨/研削は、必要性がある時に限ることが有利です。
・円筒研磨/研削の狙い3つの高精度と注意点
→「高面粗度、高精度寸法、高硬度材料研磨/研削」の3点です。
・センタレス研削のメリット
→センタレス研削は、芯出しが必要なく量産に向いています。
・円筒研削盤の研削方法/注意点
→プランジ研削、プランジ研削、アンギュラ研削があります。
・円筒研磨/研削のコストダウン、高資金効率には「工程結合」がよい。
→
「工程結合」で仕掛在庫を削減し資金効率を高める方向性が正解です。しかし、必ずしも専用機化が良いとは限らず、その後の「カイゼン」作業がしやすい工程が良いのです。
・インダストリー4.0(第四次産業革命)
→「中間在庫を削減する」工夫を進めることです。円筒研磨/研削を含めて全工程において、「カイゼン」活動を持続していくことが絶対の条件です。