深穴加工とは?BTA・ガンドリル等の種類別の加工方法と特徴を解説
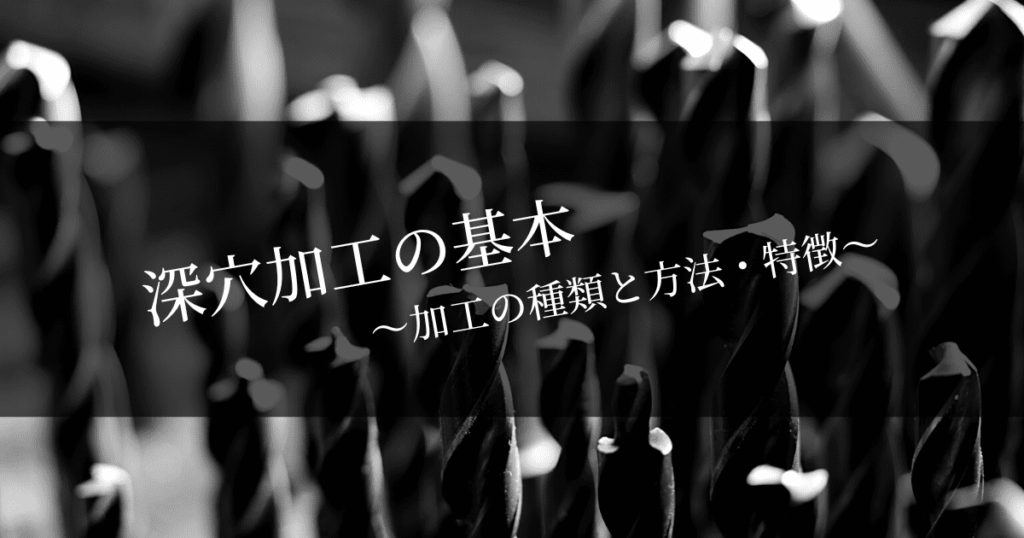
「深穴加工」とは、穴の直径の4倍以上の長さの穴をあける時に用いられる加工方法です。
「深穴加工」は、シリンダーや長尺シャフト、スピンドル、金型などの製造の際に、長い穴をあける加工方法として利用され、自動車産業、航空産業、造船業、油圧機械部品など様々な分野で必要不可欠な加工方法となっています。
この記事では、「深穴加工」方法の中から、高い加工精度で、穴の内面の仕上がりが滑らかな「ガンドリル加工」と「BTA加工」、直径0.1mm以下の微細な深穴加工が可能な「放電加工」について、概要やそれぞれの深穴加工方法、メリット・デメリットなどを詳しく解説します。
目次
深穴加工の概要
深穴加工はJIS(日本工業規格)では「一般的に長さと直径の比が4倍以上の穴をあける作業」と定義されています。
深穴加工は下記のような種類があります。
- ガンドリル加工
- BTA加工
- 放電加工
- ロングドリル加工
深穴加工は、通常より長い穴をあけることになるので、加工の速度や精度、穴の内面の仕上がりの滑らかさも重要となってきます。
「ガンドリル加工」と「BTA加工」は、「ロングドリル加工」に比べて、直進性に優れるので曲がりが少ないです。
また、切り屑の排出が容易なためステップフィードが不要で、より速く高い精度で、穴内部も滑らかに仕上がります。
「放電加工」は、直径0.1mm以下の微細な深穴加工が可能です。
「ガンドリル加工」と「BTA加工」、「放電加工」の穴の大きさによる使い分けの目安は下記の通りです。
- 0.05mm~3.0mm程度:放電加工
- 3mm~30mm程度:ガンドリル加工
- 30mm~350mm程度:BTA加工
ガンドリル加工・BTA加工・放電加工での深穴加工方法
ここでは、下記の3種類の深穴加工方法を詳しく解説します。
- ①ガンドリル加工
- ②BTA加工
- ③放電加工
①ガンドリル加工による深穴加工方法
「ガンドリル加工」は、ガンドリルの内部で長軸方向にドリルの先端部まであいた穴に、高圧の切削油を送り込んで、ドリルの先端から噴射しながら、ドリルを回転させて穴をあけていきます。
先端部で噴射される切削油により、切削部位の摩擦を低減し、摩擦熱が冷却されます。
さらに、切削により出てきた切り屑を、切削油の流れによって、ガンドリルの長軸方向に沿って彫られたV字型の溝を通して外部に排出します。
②BTA加工による深穴加工方法
「BTA加工」は、加工物に穴を開けるために回転しているボーリングバーと加工物のわずかな隙間を通じて、高圧の切削油をドリルの先端部まで到達させます。
先端部に到達した切削油により、切削部位の摩擦を低減し、摩擦熱が冷却されます。
さらに、切削によって出てきた切り屑は、ボーリングバーと加工物のわずかな隙間から、切削部位へ湧き出してくる切削油の流れにのって、ボーリングヘッドの先端に開口している穴から、パイプのように中空の構造をしたボーリングバーの内部を通じて外部に排出されます。
BTA加工による深穴加工の種類と方法
「BTA加工」には、以下の3種類の深穴加工方法があります。
- ソリッドボーリング加工
- トレパニング加工
- カウンターボーリング加工
ここでそれぞれを解説します。
ソリッドボーリング加工
「BTA加工」のなかで最も一般的で、穴のあいていないムクの材料に穴をあけるための深穴加工方法です。
穴になる部分をすべて削り取ることになります。
トレパニング加工
中心部に芯を残した状態で加工を進める方法です。
芯の部分は削る必要がないので、削る量が最小限で済みます。
そのため、機械への負担が少なく、出力が小さめの機械でも深穴加工が可能です。
カウンターボーリング加工
パイプ状など、中空の材料の穴をさらに広げるための加工方法です。
穴の内面を滑らかにきれいに仕上げたり、精度が求められたりする場合にも使用されます。
③放電加工による深穴加工方法
「深穴加工」に利用される放電加工には、「細穴放電加工」があります。
「細穴放電加工」は、絶縁性の加工液を掛け流しながら、加工物に電極を回転させながら近づけて通電し、アーク放電の火花の熱で溶かしながら穴をあけます。
アーク放電はパルス状で高頻度に行います。
放電加工と電解加工の相違点
「放電加工」は絶縁性の加工液を掛けながら、アーク放電の火花の「熱エネルギー」で加工物を溶かして穴をあけるのに対して、「電解加工」は、アルカリ性の電解液を掛けながら電極から放電し、「化学エネルギー」で加工物を溶かして穴をあける点が異なります。
ガンドリル加工・BTA加工・放電加工での深穴加工のメリット・デメリット
ここでは、ここまでで触れてきた下記の3種類の深穴加工のメリット・デメリットを解説します。
- ①ガンドリル加工
- ②BTA加工
- ③放電加工
①ガンドリル加工による深穴加工のメリット・デメリット
ガンドリル加工による深穴加工のメリット・デメリットを解説します。
「ガンドリル加工」は「BTA加工」と加工のメカニズムが似ているので、対象となる穴の大きさ以外のメリット・デメリットも似ている部分があります。
ガンドリル加工のメリット
メリット | 詳細 |
穴の直径が3mm~30mm程度の比較的小さな穴の深穴加工に適している | |
通常のドリルより長い穴をあけることができる | |
切り屑の排出性がよい | 「ガンドリル加工」ではガンドリルの長軸方向に彫られたV字型の溝から、高圧の切削油の流れにのって切り屑が外部に排出されます。 |
高い精度での深穴加工が可能 | 「ガンドリル加工」は直進性が良く、曲がりが少ないので、精度の高い深穴加工が可能です。 条件にもよりますが、芯のズレは100mmの深さの穴で、0.01mm以下と、穴の直径と共に高精度で仕上げることが可能です。 |
穴の内面が滑らかできれいに仕上がる | 切り屑がガンドリルの内部を通じて排出されるため、切り屑により、穴の内面を傷つけることがありません。 ガンドリルには先端部の側面に、ガイドパッドが付いており、バニシング効果により穴の内側の強度が上がり、滑らかにきれいに仕上がります。 |
短時間で深穴加工が可能 | 「ガンドリル加工」では切り屑を排出するために、普通のドリルのようにステップフィードを行う必要がありません。 そのため、後戻りすることなく効率的に深穴加工を行えます。 |
工具のライフサイクルが長い | 「ガンドリル」は切れ味が鈍くなってきたら、刃部の再研磨が可能です。 そのため管理が容易で、使い捨てとは異なり長く使用できます。 |
高い硬度のステンレス鋼など、難削材の深穴加工が可能 | 高硬度の難削材でも高い精度で深穴加工が可能です。 |
ガンドリル加工のデメリット
デメリット | 詳細 |
微細な穴や大きめの穴あけには適さない | 「ガンドリル加工」は穴の直径が3mm~30mm程度の比較的小さな深穴加工に適しているので、それ以外の大きさの穴の加工には適しません。 |
高い精度を担保するには高い技術が必要 | 穴あけの条件調整はもちろんのこと、加工物の前処理にも高い技術と精度が必要です。 |
②BTA加工による深穴加工のメリット・デメリット
BTA加工による深穴加工のメリット・デメリットを解説します。
「BTA加工」は「ガンドリル加工」と加工のメカニズムが似ているので、対象となる穴の大きさ以外のメリット・デメリットも似ている部分があります。
BTA加工のメリット
メリット | 詳細 |
穴の直径が30mm~350mm程度の中径~大径の深穴加工に適している | |
通常のドリルより長い穴を開けることができる | |
切り屑の排出性がよい | 「BTA加工」ではパイプ状で中空のボーリングバーの内部を通じて、高圧の切削油の流れにのって切り屑が外部に排出されます。 |
高い精度での深穴加工が可能 | 「BTA加工」は直進性が良く、曲がりが少ないので、精度の高い深穴加工が可能。 |
穴の内面が滑らかできれいに仕上がる | 切り屑がボーリングバーの内部を通じて排出されるため、切り屑により穴の内面を傷つけることがありません。 |
短時間で深穴加工が可能 | 「BTA加工」では切り屑を排出するために、普通のドリルのようにステップフィードを行う必要がありません。 そのため、後戻りすることなく効率的に深穴加工を行えます。 |
高い硬度のステンレス鋼など、難削材の深穴加工が可能 | 高硬度の難削材でも高い精度で深穴加工が可能です。 |
BTA加工のデメリット
デメリット | 詳細 |
小さめの穴あけには適さない | 「BTA加工」は穴の直径が30mm~350mm程度の中径~大径の深穴加工に適しているので、それより小さい径の深穴加工には適していません。 |
高い精度を担保するには高い技術が必要 | 穴あけの条件調整はもちろんのこと、加工物の前処理にも高い技術と精度が必要です。 |
③放電加工による深穴加工のメリット・デメリット
放電加工による深穴加工のメリット・デメリットを解説します。
放電加工のメリット
メリット | 詳細 |
極細の穴をあけることができる | 他の深穴加工ではできないような、穴の直径が0.1mm以下の極細の穴をあけることができます。 |
加工物の硬度が高い難削材でも加工できる | アーク放電の熱で溶かしながら穴をあけるので、加工物の硬さに関係なく深穴加工が可能です。 |
加工物に接触することなく穴をあけるので、圧力などの負担がかからない | 電極を加工部位に近づけて接触することなく穴をあけるので、他の深穴加工とは異なり、圧力などの負担がかからない。 |
冷却効率良く加工が行える | 絶縁性の液体を掛け流しながら、効率良く局所的に発生するアーク放電の熱を冷却できます。 |
バリがでにくい | アーク放電の熱で溶かしながら穴をあけるのでバリが出にくいです。 |
放電加工のデメリット
デメリット | 詳細 |
加工に時間がかかる | アーク放電の熱で少しずつ溶かしながら穴をあけるので、加工に時間がかかります。 そのため、大量生産には適しません。 |
導電性の素材しか加工できない | 電極と加工物の間に電流を流す必要があるので、電気を通さない加工物には「放電加工」は行えません。 |
まとめ
「深穴加工」のなかでも、「ロングドリル加工」などとは異なり、仕上がりが滑らかで、精度が高く、加工が速い、「ガンドリル加工」と「BTA加工」、極細の深穴加工が可能な「放電加工」について、詳しく解説してきました。
重要なポイントとしては、穴の大きさにより下記のような使い分けをすることがあげられます。
- 0.05mm~3.0mm程度:放電加工
- 3mm~30mm程度:ガンドリル加工
- 30mm~350mm程度:BTA加工
上記のことを含め、深穴加工を行う際はこの記事を参考に方法を選択いただければ幸いです。