研削加工とは?特徴・種類・加工時の注意点や、切削・研磨との違いについて
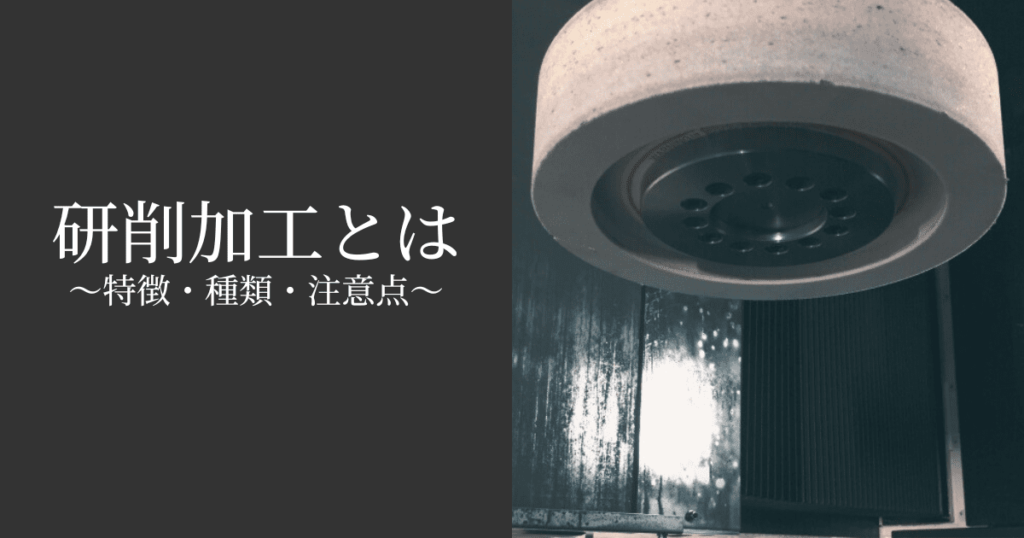
研削加工とは、砥石を使って材料の表面を削る、除去加工のひとつです。
同じ除去加工には切削加工や研磨加工も分類されますが、これらは目的によって使い分けられます。
この記事では、そんな研削加工の特徴や種類、加工時の注意点や切削加工・研磨加工との違いなどについて解説します。
目次
研削加工とは
研削加工とは、研削盤という機械を使い、砥石を高速回転させて、これを材料に押し当てることで、表面を削る加工です。
砥石は砥粒という硬く鋭い粒を固めたもので、これが刃物の役割を果たし、材料の表面を少しずつ削ります。
なお、この砥粒は徐々に削る力を失います。
しかし、このように削る力を失うと、脱落して下から新しい砥粒が現れます。
これにより、砥石は削る力を維持することを可能としています。
そんな研削加工は、切削加工では難しい超硬合金や焼き入れ後といった硬度の高い材料も削ることができ、また少しずつ削るため時間はかかるものの、高い精度で削ることも可能です。
なお、研削加工の特徴については、次で解説します。
研削加工の特徴
研削加工の特徴を、メリットとデメリットに分けて解説します。
研削加工のメリット
寸法精度が高い | 砥石を高速回転させて、少しずつ削るため、高い寸法精度で削ることができます。 |
硬度の高い材料も加工できる | 砥石は砥粒という刃物となる粒を高めたものです。 そしてこれは削る力を失うと下から新しい砥粒が現れます。 これにより削る力を維持できるため、硬度の高い材料も加工することができます。 |
材料の表面をなめらかに仕上げられる | 砥石に含まれる無数の細かい砥粒で少しずつ削るため、材料の表面を滑らかにすることができます。 仕上げ処理として用いられることもあります。 |
陶磁器などの材料も加工できる | 超硬合金や焼き入れ後といった硬度の高い材料に加え、少しずつ削るため陶磁器などの脆性材料も加工できます。 |
研削加工のデメリット
加工に時間がかる | 高い精度で削ることができる反面、少しずつ削るため時間がかかってしまいます。 そのため、基本的には切削加工で大きく削り、研削加工で小さく削るという手順を踏みます。 |
加工時に熱が発生する | 高速回転させた砥石を材料に押し当てて削るため、摩擦により熱が発生します。 これにより焼けやワレが発生するおそれがあるため、一般的には研削液で冷却しながら加工します。 |
複雑な加工面は削れない | 砥石を押し当てる面が加工の対象となります。 そのため、研削盤にもよりますが、複雑な加工面は削ることができません。 |
研削加工の種類
研削加工といっても、以下のようにいくつか種類があります。
- 平面研削
- 内面研削
- 円筒研削
- センタレス研削
- ホーニング加工
- プロファイル研削
- 歯車研削
それぞれについて簡単に解説します。
平面研削
平面研削は、材料の表面を平面に削る加工です。
平研(ひらけん、へいけん)とも呼ばれます。
平面研削盤のテーブルの上に材料を固定して、高速回転する砥石を上から押し当てます。
テーブルを動かせるパターンと砥石を動かすパターンがあり、幅広いサイズに対応が可能です。
内面研削
内面研削は、円筒形状の材料の内面を削る加工です。
内研(ないけん)とも呼ばれ、高い寸法精度の穴の内面が求められる場合に用いられます。
砥石と材料をそれぞれ逆方向に回転させて、穴の内面を削ります。
なお、砥石のみを回転させるプラネタリ形と呼ばれる方法もあり、これは材料を回転させられない場合に用いられます。
円筒研削
円筒研削は、円筒形状の材料の表面を削る加工です。
軸を固定した材料を高速回転させて、その表面に同じ方向に回転させた砥石を押し当てます。
部品同士の接触部となる摺動部において、摩擦軽減を目的に用いられます。
センタレス研削
センタレス研削は、円筒研削と同じように円筒形状の材料の表面を削る加工です。
しかし、円筒研削のように完全に固定しない、という点で異なります。
センタレス研削は、回転する砥石と調整車、支持刃の3点で材料を支えて、加工します。
材料を完全に固定する必要がないことから大量生産向きで、また均等に支えるため均一な仕上がりになることが特徴です。
ホーニング加工
ホーニング加工は主に、内面研削と同じように円筒形状の材料の内面を削る加工です。
砥石を装着した円柱形状の工具(マンドレル)が材料の内面で均等に広がり、回転また往復運動します。
そのため、内面研削よりも高い寸法精度を実現することが可能です。
また、クロスハッチになるため、摺動性がよくなる特徴も持ちます。
プロファイル研削
プロファイル研削は、製品の投影図に材料を影絵のように拡大して映します。
そして、投影図に従って、手動またプログラム制御で材料を加工します。
直線、曲線、テーパ、溝などが複雑かつ不規則な場合でも、高い寸法精度で加工することが可能です。
歯車研削
歯車研削は、円盤形状やネジ形状の高速回転する砥石で、歯面を削る加工です。
歯車の寸法精度を高める、歯車から出る騒音を低減させる、歯車の寿命を延ばすといった効果があります。
歯車加工の仕上げ処理の工程で用いられます。
切削加工・研磨加工との違い
研削加工は除去加工に分類されますが、同じように切削加工や研磨加工も除去加工に分類されます。
しかし、これらは同じ除去加工ではあるものの、目的によって使い分けられます。
そこで、研削加工と、切削加工・研磨加工との違いを解説します。
なお、金属加工全般については以下の記事で解説していますので、ぜひ合わせてチェックしてみてください。
▼関連記事
金属加工とは?加工の種類や方法・選び方のポイントを紹介!
切削加工との違い
切削加工は、刃物(工具)で材料を削る加工です。
刃物が材料に食い込むため、大きく削ることができます。
一方研削加工は、砥石を使って材料の表面を少しずつ削るため、まずこの点が違います。
そして、これにより精度にも大きな違いが生まれます。
研削加工は砥石に含まれる無数の細かい砥粒で削るため、材料の表面をなめらかに仕上げることが可能です。
しかし切削加工では、そこまでの精度は求められません。
なお、加工にかかる時間に関しては切削加工に軍配が上がります。
以上のことから、切削加工は大まかに削って形状を作る目的、研削加工はそれを少しずつ削って高い精度に仕上げるという目的で用いられる、となります。
研磨加工との違い
研磨加工は研削加工と同じように、材料の表面を少しずつ削る加工です。
しかし、研磨加工は流動する粒子によって材料の表面を削るのに対し、研削加工は刃物の役割を果たす硬く鋭い砥粒で削ります。
このことから、それぞれ目的としては、研磨加工は材料の表面に光沢を出すように磨く意味合いが、研削加工は材料の表面を削って整える意味合いが強いです。
とはいえこれらの言葉は、実際の現場では同じ目的の意味合いで使われることも多いようです。
研削加工時の注意点
目詰まり | 砥石の表面の砥粒の間に、削りかすが詰まり、切れ味が悪くなる現象です。 また、削りかすが排出されなくなることにより熱がこもり、焼けなどが発生するおそれがあります。 |
目つぶれ | 砥石に含まれる砥粒が、削る力を失っても脱落しない現象です。 これにより摩擦面が広くなるため、焼けなどが発生するおそれがあります。 |
目こぼれ | 砥石に含まれる砥粒を固めている結合剤がやわらかいときに起きる現象です。 これにより、まだ削る力を持っているにもかかわらず、砥粒が脱落してしまいます。 その結果、砥石の表面が荒れ、材料の表面の仕上がりも悪くなってしまいます。 |
まとめ
研削加工は、研削盤を使い、砥石を高速回転させて、これを材料に押し当てることで、表面を少しずつ削る加工です。
寸法精度高く、材料の表面をなめらかに仕上げることができ、また硬度の高い材料も削ることができる特徴を持ちます。
なお、研削加工の依頼なら、当サイトJig Matchにお任せください。
製品や部品を製作してほしい方は
①無料会員登録
②図面をアップロード
というステップを踏むだけで全国の加工業者からまとめて見積りを取ることができます。
また、見積りを取るだけでなく、発注から納品までワンストップで済ませることが可能です。
詳しくはぜひ以下のバナーからチェックしてみてください。