研磨加工とは?種類や手順、研削との違いを解説
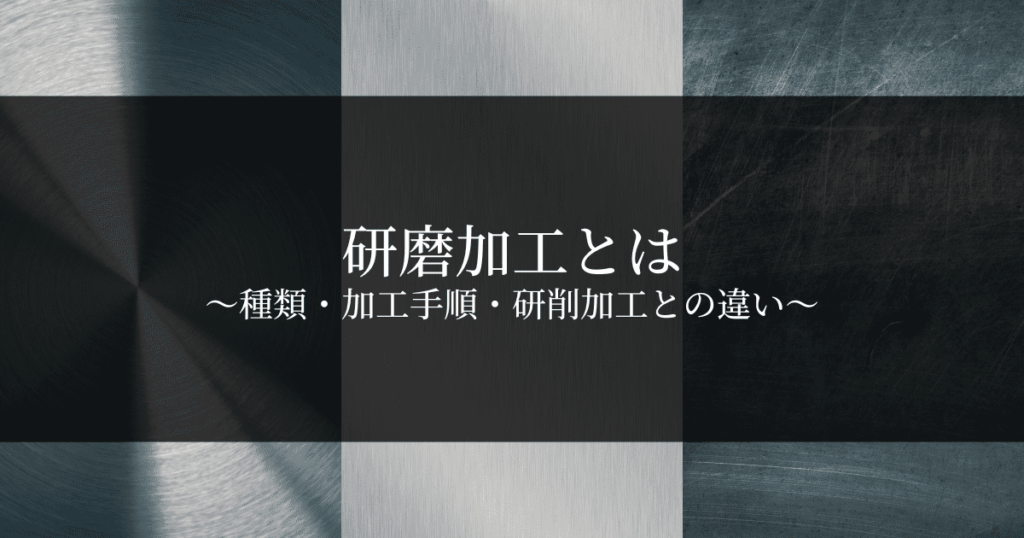
金属を加工する際に、最終的な仕上げの工程で行われる「研磨加工」。
「研磨加工」は、表面的な寸法を高い精度で微調整できますが、前加工の精度に依存している点にも注意が必要です。
また、「研磨加工」により、表面がなめらかになり、ツヤが出て、見た目も美しく仕上げることができます。
さらに、表面がなめらかになることにより、サビや汚れに強くなるなど、たくさんのメリットがあります。
この記事では、「研磨加工」の基礎知識から、研削加工との違い、種類や加工手順などを詳しく、網羅的に解説します。
目次
研磨加工とは?
「研磨加工」は、主に金属加工の時に、最終的な仕上がりを、高い精度で微調整できる加工方法です。
そのため、精度の大まかな調整には適さないので、前加工の精度もおろそかにできません。
そんな「研磨加工」には、下記の2通りの方法があります。
どちらの加工方法でも、表面がなめらかになり、高い精度で微調整ができます。
「研磨加工」は、材料の表面を少しずつ削ったり、溶かしたりできるので、マイクロメートル(μm)単位(1マイクロメートルは1/1000mm)での微調整が可能です。
「研磨加工」により、最終的な仕上げで要求される「高い寸法精度」、「美しい外観」、「サビや汚れに強い」、など数多くの条件を満たすことができるので、製品の付加価値を高めることができます。
研磨加工と研削加工の違い
「研磨加工」と「研削加工」の違いについて、「目的」と「加工方法」の両面から説明します。
それに対して、「研削加工」は「研磨加工」より前の工程で、「研磨加工」より大まかな寸法精度の調整に利用される加工方法です。
「研磨加工」は、材料に圧力を掛けて砥粒に押しつけた状態で動かしたり、砥粒は使わずに電気分解を利用したりして、表面を少しずつ削ります。
それに対して、「研削加工」は材料に、高速回転する砥石を当てて削る加工方法です。
研磨加工の分類と種類
「研磨加工」は加工方法の特徴により下記の3種類に分類されます。
- ①固定された砥粒での研磨加工
- ②遊離した砥粒での研磨加工
- ③砥粒を使わない研磨加工(電気分解による加工)
以下から、これら3種類に属する加工方法について詳しく解説します。
①固定された砥粒での研磨加工
砥粒が接着剤で固められた研石、砥粒が接着された紙や布などを、機械に取り付けて行う研磨加工の方法です。
砥石研磨
「砥石研磨」は高速回転する砥石に材料を押し当てたり、固定した砥石に材料を動かしながら押し当てたりして、表面をなめらかにする加工方法です。
「砥石研磨」はどちらかと言えば、「研磨加工」というよりは「研削加工」に近いでしょう。
たとえば、グラインダーやサンダーなどの研磨機を利用するものから、身近な例で言えば、包丁やナイフなどを研石で研ぐ場合も、「砥石研磨」に相当します。
砥石は砥粒を結合剤で固めたもので、「砥石研磨」により、砥石表面の砥粒の角が徐々にとれます。
しかし、材料との摩擦で、砥石表面から摩耗した砥粒が脱離することで、新たに鋭利な砥粒が砥石表面に露出し、研ぎ味は一定に保たれます。
ホーニング加工
「ホーニング加工」は、エンジンや油圧機械のシリンダーのような、円筒状の部品内面を、高い精度で研磨し、なめらかに仕上げる加工方法です。
加工時には、砥石をホーニングヘッドというホルダーに装着し、円筒状部品の内部に挿入し、砥石を円筒内面に密着させ、押しつけます。
この状態で、ホーニングヘッドを回転させながら上下運度も加え、内面を精密に研磨して仕上げます。
また、この「ホーニング加工」により「クロスハッチ」と呼ばれる網目状の超微細な筋を入れることもできます。
シリンダー内面で、ピストンの可動域に、くまなく刻まれた「クロスハッチ」は、筋の溝に潤滑油をキープすることで、シリンダー内面を潤滑油でなじませ、ピストンとの摩擦を軽減します。
「ホーニング加工」は、このように、シリンダーに高い機能性を付与し、付加価値を高めます。
加えて、「ホーニング加工」は円筒状部品だけではなく、歯車の精密加工の仕上げとしても利用されています。
最近では自動車産業などでも静音性が重視されています。
そのため、歯車の歯面のかみ合わせを改善し、ギアのノイズや振動を低減できる「ホーニング加工」は、ギアの付加価値を高める重要な加工技術となっています。
- 真円度・円筒度の精度が高い
- 寸法精度が高い
- 加工面のクロスハッチを調節可能
- なめらかな仕上がり
- 材料への負担が少ない
- 前加工の精度を大幅に修正できない
- 穴径に合った工具が必要
それに対して、「ホーニング加工」は大まかな精度の修正には向いていませんが、材料の表面を精密に整え、高い精度で研磨して仕上げることができます。
そのため、前加工の加工精度が重要となってきます。
▼ホーニング加工について詳しく解説している記事
ホーニング加工とは|加工機について・加工の特徴や注意点・内面研磨/研削との違い
研磨布紙加工
「研磨布紙加工」は、砥粒が接着された紙や布を使用して材料を研磨する加工方法です。
身近な例で言えば、紙やすりを使用した研磨などが相当します。
工場などの現場では、輪っか状の研磨ベルト(表面に砥粒が接着されたベルト)を回転させ、そこに、材料を当てながら、研磨を行います。
②遊離した砥粒での研磨加工
工具などに砥粒が固定されておらず、砥粒が液体と混合されて遊離した状態で、材料表面を研磨する方法です。
ラップ加工
「ラップ加工」は「ラッピング加工」とも言われます。
「ラップ加工」は、ラップという水平の盤の間に材料を設置して圧力をかけ、ラップと材料のわずかな隙間に入り込んだラップ剤、つまり砥粒を擦り合わせることで、研磨する加工方法です。
ラップ剤は、砥粒と少量の潤滑油を混ぜ合わせたものです。
ベアリングなどの精密部品の最終的な仕上げや、ウェハーなど加工が難しい材料の表面処理に利用されます。
「ラップ加工」は、材料の加工面を高い平面度に加工できるだけではなく、反対側の面と高い精度で平行になるように加工できる点がメリットです。
しかし、加工に時間がかかるのがデメリットです。
なお、「ラップ加工」は、「乾式ラッピング」と「湿式ラッピング」の2種類があります。
それぞれ下記で解説します。
ラップ表面の微細な凸凹にはまり込んで、半固定状態の砥粒の上を、材料がすべることで研磨されます。
「湿式ラッピング」より、削られる量が少ないので、研磨の精度が高く、仕上がりの表面はなめらかで、光沢が出ます。
ラップと材料のわずかな隙間に浸透した砥粒が、液体の中で転がりながら材料の表面を研磨します。
「乾式ラッピング」より、削られる量が多いので、粗めで無光沢になります。
そのため、荒仕上げなどの工程で利用される加工方法です。
▼ラップ加工について詳しく解説している記事
ラップ加工とは?原理・ラップ盤やラップ剤・メリットとデメリットを紹介!
バレル研磨
「バレル研磨」は、その名の由来の通り、バレル(樽)のような研磨容器に、材料と共にメディア(研磨石など)とコンパウンド(潤滑剤)を入れます。
そして、研磨容器を回転させたり、振動させたりして、材料と研磨石との接触を促し、材料表面のバリ取りや面取りを行います。
加工精度はあまりよくありませんが、一度に大量の材料の加工を行えるので、高い精度が要求されない部品の大量生産に向いています。
▼バレル研磨について詳しく解説している記事
バレル研磨とは|メリット・デメリットと4つの加工方法、バフ研磨との違いを解説
ポリシング研磨(バフ研磨)
「ポリシング研磨」は、研磨剤を付けたバフと呼ばれる工具を高速回転させて、これを材料に押し付けることで研磨する加工方法です。
バフ研磨とも呼ばれます。
ポリッシャーやディスクグラインダーなどの工具を使う場合もあり、つや出しや鏡面仕上げなどに用いられることが多いです。
鉄やステンレス、アルミやチタンなどの金属に加え、プラスチックなどの樹脂や、ガラスに対して行うこともできます。
なお、「ポリシング研磨(バフ研磨)」は手作業で行われるため、大量生産には向いておらず、またコストも高い傾向にあります。
▼ポリシング研磨(バフ研磨)について詳しく解説している記事
バフ研磨とは?効果や種類・注意点を解説
③砥粒を使わない研磨加工(電気分解による加工)
砥粒は使用せずに、電気分解の作用で材料の表面を溶かす加工方法です。
電解研磨
「電解研磨 」は材料を電解液に浸して電流を流し、電気分解の作用で、材料表面の凸凹の凸部分を優先的に溶かします。
これにより、非常に高い精度で、材料表面を平坦になめらかに仕上げます。
他の研磨加工では研磨できないような、狭い場所や、超微細な凸凹も平坦化します。
これにより、鏡面のようにピカピカに仕上がるだけでなく、ステンレスなどの材料では、サビヘの耐性も向上します。
このように、非常に加工精度も高く、サビや、汚れの付着に対する耐性が著しく向上するなど、製品の付加価値を高めます。
一方で、ステンレスやアルミ、チタンなど適用できる金属が少なく、高コストなどのデメリットもあります。
▼電解研磨について詳しく解説している記事
電解研磨とは?原理と加工方法・メリットデメリットを紹介
研磨加工の加工手順
「研磨加工」の加工手順には下記の4つの工程があります。
- ①下地
- ②ならし
- ③つや出し
- ④鏡面仕上げ
初めは粗めの砥粒で大まかに下地を整え、後の工程に進むに従って、細かな砥粒を使用し、より精度を高く、滑らかできれいな仕上がりに近づけていきます。
以下で、上記の4つの工程を詳しく解説します。
①下地
「下地」の工程では、粒子径の大きな粗めの砥粒を用いて、材料表面の大きめの凸凹や、汚れなどの付着物を除去します。
「下地」では、いきなり最終的な加工精度を狙うというよりは、仕上げの土台となる下地をしっかり整えることを意識して、細部は気にせず大まかに削ります。
ただし、必要以上に粗い砥粒で削ると、仕上がりの寸法精度に影響を与えるような深い傷が入ることがあるので、適切な粒度の砥粒を選ぶことが大切です。
②ならし
「ならし」の工程では、「下地」の工程で粗く削られたざらざらした表面をみがいて、平らにならします。
「ならし」の工程は、「つや出し」や「鏡面仕上げ」など、最終的な仕上げに関わる工程に大きな影響を与えます。
そのため、仕上げの工程で修正できないような、大きな凸凹や深い傷が残らないように、均等に磨きをかけて平坦にならすようにします。
③つや出し
「つや出し」の工程では「ならし」で平坦になった表面を、さらになめらかに仕上げます。
そのために、「ならし」の時より細かい粒度の砥粒を使用して、表面の汚れを落とし、細かな凸凹を平坦に整え、つやを出します。
「つや出し」では、ヘアライン加工のように材料の表面にあえて、デザイン性の高い微細なキズを付け、オシャレなつや消し加工を行うこともあります。
④鏡面仕上げ
「鏡面仕上げ」の工程では、読んで字のごとく、一点の曇りもない鏡のように、美しい光沢を放つ表面に仕上げます。
砥粒の細かさを段階的に小さくしていくことで、最終的な仕上がりを微調整できます。
前工程までで、すでにお膳立ては済んでいるので、比較的簡単に仕上げることができます。
言い方を変えれば、「鏡面仕上げ」の最終的な仕上がりは前工程までの精度に依存しているので、1~3の工程を丁寧に行う必要があるということです。
まとめ
「研磨加工」は、製品の最終的な仕上がりを高い寸法精度で、なめらかに、美しくする加工方法です。
「研磨加工」は下記の3タイプに分類されます。
- ①固定された砥粒での研磨加工
- ②遊離した砥粒での研磨加工
- ③砥粒を使わない研磨加工(電気分解による加工)
さらに、下記の7つの研磨加工方法を解説しました。
- 砥石研磨
- ホーニング加工
- 研磨布紙加工
- ラップ加工
- バレル研磨
- ポリシング研磨(バフ研磨)
- 電解研磨
この記事を読んでいただき、上記7つの研磨加工方法の特徴やメリット・デメリットを参考に、ご自身の製品に最適な研磨加工の方法を見つけていただければ幸いです。
部品製作を依頼したい方と、依頼を受けたい方をつなぐマッチングサービスです。
-
▼メリット
▽製作依頼者様
・依頼先が見つかる
・全国の加工業者から見積りを取れる
▽加工業者様
・営業なしで仕事が見つかる
・自社の得意、また向いている仕事を選べる
登録料や年会費は無料、取引が成立するまで費用はかかりません!
ぜひ以下のバナーから詳細をご確認ください!